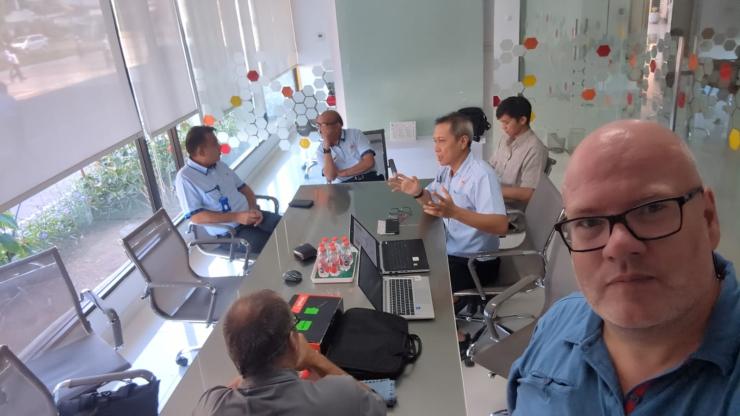
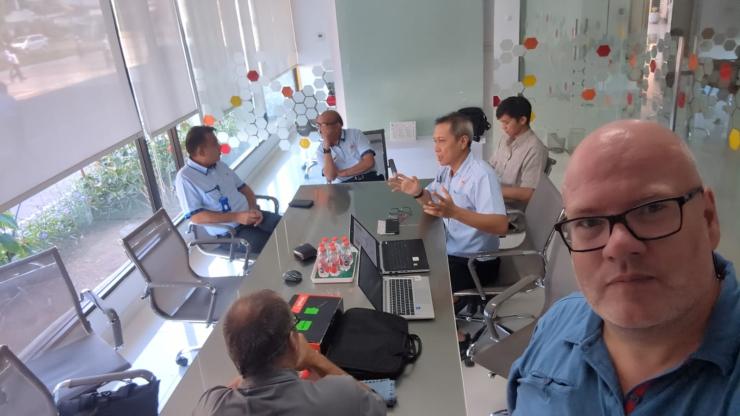
EnaTex: project teams travel to Indonesia
On-site measurements to determine material and energy flows were carried out at two sites of the EnaTex project partners PT Sri Rejeki Isman Tbk (SriTex) and PT Harapan Kurnia. The aim of the EnaTex work was to comprehensively record all relevant input and output flows in order to determine the efficiency and thus the fuel efficiency of the combustion systems analysed at the production sites.
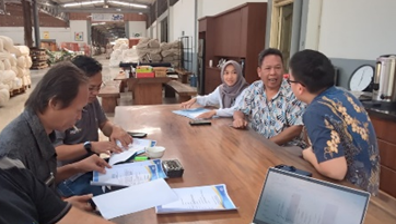
Focus topic "textile"
In 2023, EnaTex presented the first optimisation proposals for saving energy in the dyeing process for cotton knitwear through the use of innovative, efficient dyes, which are already being implemented in a large number of colour shades, especially for export goods. In addition to energy savings in the heating of washing baths after dyeing, large quantities of water are saved, reducing the amount of waste water that needs to be treated. The carbon footprint can be reduced by two-thirds from 0.520 to 0.171 kg CO₂ equivalent per kilogram of fabric during the washing process for dark colours alone. This can save around 1,000 kg of CO2 equivalents per year in the production of dark colours.

Focus topic "CSR"
The "CSR team" (Corporate Social Responsibility) also continued its intensive dialogue with local Indonesian partners. This included in-depth interviews with production managers at Harapan Kurnia and a survey of 100 employees on occupational safety. The next step will be to roll out the health and safety training programme developed specifically for the EnaTex project - which has already been successfully implemented at project partner Sritex - at Harapan Kurnia by the end of the project. The results of the data analysis from both companies will be presented at the final EnaTex event in 2025.
Unfortunately, the visit to Solo/Surakarta was overshadowed by the news of the imminent bankruptcy of the industrial partner Sritex. The latest research results on viscose fabrics were also presented there, but their realisation is currently in doubt.

Focus topic "measuring“
In collaboration with experts from the Textile University Politeknik STTT Bandung and engineers from partner textile companies, data was collected on the energy efficiency of two steam generators and a thermal oil heater. All systems are fully fuelled with local coal. Harapan Kurnia also burns dried sewage sludge. Combustion is either fluidised bed or grate firing, with both systems having different fuel requirements and very different combustion dynamics. The steam produced is used to heat wet processing equipment such as washing machines, bleachers, steamers or polyester dyeing plants. The heat is removed by condensing the saturated steam produced to heat the aqueous medium. Hot air is required for dry finishing, which includes stretching, drying or fixing processes. Temperatures of up to 200°C can be generated using oil/air heat exchangers.
To ensure the correct balance of material and energy flows, the location-based data was subjected to a quality check and measurements were repeated where necessary. At the same time, the Indonesian partners recorded all digital and manual data and readings. Where data was not available, video recordings were made for later analysis.

An initial assessment and discussion with all partners identified the need for continuous, preferably digital, data collection and analysis, as well as ongoing maintenance and testing of sensors and technology. All boiler systems are currently fired with low cost, low calorific Indonesian lignite. Other objectives include the collection of environmental impact data, such as flue gas measurements and elemental analyses of the lignite, bottom ash and fly ash. The results will be discussed with technical staff and managers, and will be categorised as organisational, low-investment and investment-intensive. This will be followed up at the IZES office in Saarbrücken.
As part of the measurement campaigns, the German partners explained the operation and function of the measuring devices, enabling the employees to carry out flue gas measurements independently in the future. The aim is to raise awareness of the need for continuous monitoring and control of the process technology in order to generate information on the operation of the boiler and to indicate possible interventions.

The work was fully completed during the trip. The evaluation was carried out in close cooperation between the Indonesian and German project partners. The results and the resulting recommendations for action will be presented at the final conference in Jakarta in February 2025 and discussed with representatives from politics, business and science during a two-day event.
Further information on EnaTex can be found on the project page.