Climate action
Responsible consumption and production
Partnerships for the goals
Coordinator: Fraunhofer-Institut für Grenzflächen- und Bioverfahrenstechnik (IGB)
Contact: Dr. Lénárd-István Csepei
Address: Schulgasse 11a, 94315 Straubing
Phone: +49 9421 9380-1003
Email: lenard-istvan.csepei(at)igb.fraunhofer.de
Project Partners in Germany:
- Juchheim Laborgeräte GmbH
- Hitec Zang GmbH
Project Partners in South Africa:
- EPCM Global Engineering (Pty) Ltd, Centurion, South Africa
- PPC Cement SA (Pty) Ltd, Johannesburg, South Africa
- Carbon Process Plant and Engineering S. A. Rodange, Luxembourg
- Omnia Holdings Ltd, Sandton, South Africa
- HySA Infrastructure CoC, Potchefstroom, South Africa
- c*change, Rondebosch, South Africa
Converting CO2 from hard-coal-fired power plants using green ammonia in South Africa
Hard to decarbonise branches of the industry in South Africa not only emit vast quantities of CO2 but harmful nitrogen oxide (NOx), sulphur oxide (SOx) and particulate matter as well. In order that coal can be used in as environmentally-friendly a manner as possible, until such a time as South Africa has fully converted to renewable energies, the CoalCO2-X(TM) programme aims to make flue gas components usable in the recycling-oriented manufacture of fertilisers and chemicals. Green ammonia plays a key role in this respect; Fraunhofer IGB demonstrates its synthesis within the project.
Challenges in South Africa
As a signatory of COP21, the Paris Agreement on climate change, South Africa has committed to reducing its CO2 greenhouse gas emissions. As such, the South African Ministry of Natural Resources and Energy announced the development of renewable energies and the shutdown of numerous fossil fuel power plants in its Integrated Resource Plan 2019.
In order to cover the high energy demand, a number of hard-coal-fired power plants will continue to play a role in the supply of energy even after 2030. The hard-coal-fired plants used to generate power and manufacture cement and paper emit large quantities of greenhouse gas CO2, while simultaneously releasing harmful nitrogen oxide (NOx), sulphur oxide (SOx) and particulate matter. The intensification of agriculture over the last two decades has driven up demand for fertilisers. With domestic production lagging behind on account of an outdated infrastructure, South Africa currently imports more than 60 percent of its required nitrogen fertiliser.
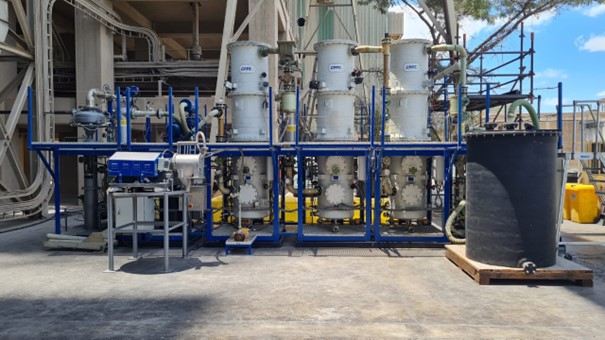
South African-German sustainability programme
With the CoalCO2-X(TM) programme, organised by the South African Department of Science and Innovation (DSI) and co-financed by the German Federal Ministry of Education and Research (BMBF), South Africa hopes to reduce the environmental footprint of sectors in which the reduction of emissions has proven difficult. The programme aims to make use of the problematic components of exhaust gas from carbon combustion as a raw material for the recycling-oriented and value-creating manufacture of products, thereby cleaning the exhaust gas. Doing so requires green ammonia, which has thus assumed a key role in the decarbonisation of the (agro)chemicals and energy industry.
Harnessing flue gas – with green ammonia
Funded by the DSI and coordinated by EPCM Global Engineering, the South African sub-project pursues the objective of demonstrating the capture of CO2, NOx, SOx and particulate matter from flue gas at a production site operated by a large-scale cement manufacturer, at a rate of 300 m3/h. The captured gases are converted into synthetic diesel fuel and various chemical precursors: ammonium bicarbonate, potassium carbonate, nitric acid and sulphuric acid. Omnia is developing a formulation which will use the extracted inorganic salts to produce marketable fertilisers.
On the German side, the BMBF is funding a CoalCO2-X(TM) sub-project coordinated by Fraunhofer IGB. The focus here is on a pilot project to test the synthesis of green ammonia using the Haber-Bosch process, at a rate of 1 kg/h. The required green hydrogen is generated via electrolysis in the plants operated by HySA (Hydrogen South Africa). Besides developing the technology and optimising the process for intermittent operation, the project team will conduct an economic assessment to support the scaling of ammonia synthesis.
Ammonia is processed with the sulphuric acid extracted from flue gas to produce ammonium sulphate, a marketable base chemical and valuable fertiliser. Green hydrogen and green ammonia thus represent important links between the technologies developed within the scope of the programme.
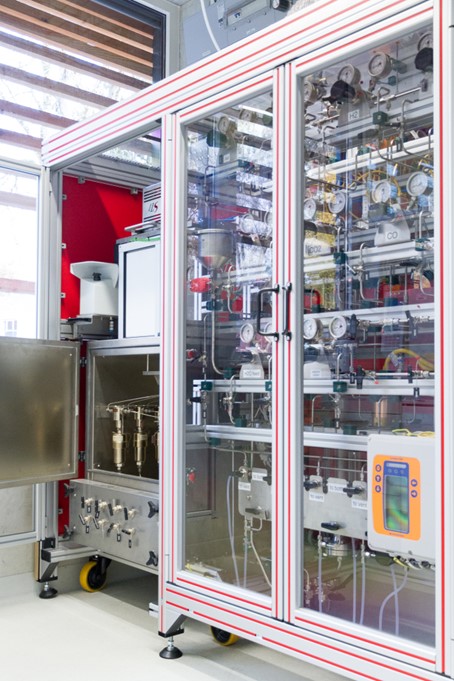
SDGs and the national hydrogen strategy
The project team has adopted the words of S.E. Maria Fernanda Espinosa Garcés, President of the 73rd session of the UN General Assembly (2018), as the motto for the cooperation between Fraunhofer IGB and its South African partners: "Let us dedicate our best efforts to accelerating the implementation of Africa's development agenda. Let us not only talk about Africa, but let us also act with Africa". These words form the moral framework for the scope of the efforts, objectives and intended effects of the project.
The project addresses technological developments (SDG 9 Industry, Innovation and Infrastructure), with a view to achieving circular and sustainable processes (SDG 12 Responsible Consumption and Production). An intercontinental, German-South African partnership has made cooperation within the project possible on a political, academic and technical level (SDG 17 Partnerships for the Goals).
The project is also in line with the German national hydrogen strategy:
- Measure 14 (Decarbonisation of the industry),
- Measure 17 (Industry-specific dialogue with stakeholders for the development of long-term strategies to decarbonise energy-intensive industries),
- Measure 24 (Cooperative demonstration project for the recovery of renewable hydrogen using modular and robust systems) and
- Measure 25 (Feasibility study regarding the use of green ammonia technology in South Africa, taking into account the local energy landscape, and ultimately, the development of an international R&D network, which will open up new markets for the export of German technology).